Reducing operational costs is a continuous priority for companies managing complex infrastructure. One of our clients in the telecom industry faced a recurring challenge: unnecessary field interventions triggered by automated alerts from network equipment. Many of these alerts did not require immediate action — some even resolved themselves. What if there was a way to intelligently filter and prioritize them?
That question led to the creation of the Ticket Allocation project — a scalable automation solution that streamlines work order dispatching and dramatically reduces operational expenditure.
The Challenge: Too many Alerts, Too Few That Matter
In a typical telecom setup, field equipment constantly communicates its status to centralized systems. When issues are detected, they generate Work Orders (WOs) that are sent to field teams for troubleshooting. However, not all alerts are critical. Some equipment regenerates without human intervention, while others trigger alerts that don’t impact network performance.
The result? Unnecessary site visits, increased costs, and reduced efficiency.
Our client wanted a way to distinguish between urgent and non-urgent interventions — automatically — before committing field resources.
The Solution: Delay Logic Based on Smart Criteria
The Ticket Allocation project automates decision-making in the WO process. It integrates several client systems to:
- – Identify the site and contextual information related to each WO
- – Apply business logic based on site-specific parameters
- – Perform additional system checks to assess actual urgency
- – Introduce a calculated delay to WOs that don’t require immediate action
This delay prevents premature dispatching, giving equipment time to recover or allowing further analysis, thus reducing avoidable interventions.
Implementation in Three Phases
The project unfolded in three phases:
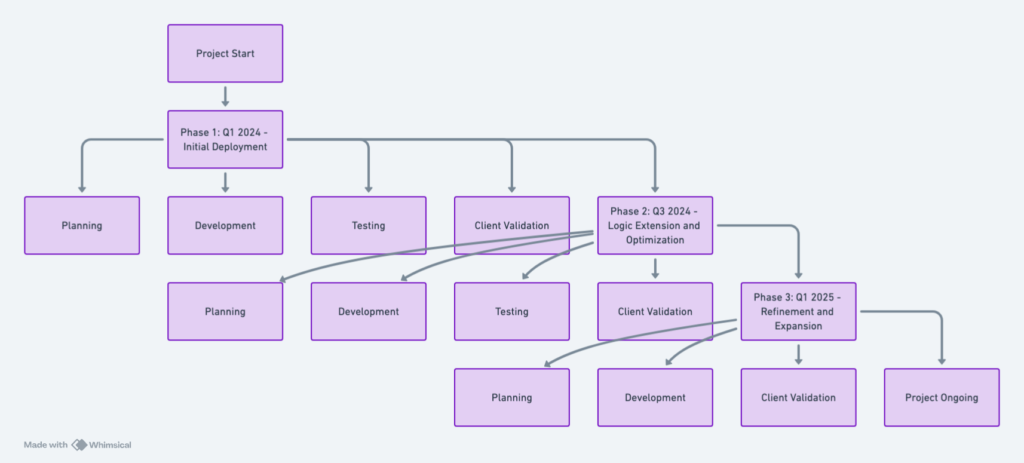
- – Phase 1 (Q1 2024): Initial deployment covering the full WO flow
- – Phase 2 (Q3 2024): Extension of logic to specific WO types and process optimization
- – Phase 3 (Q1 2025): Currently in testing, adding refinements based on feedback and expanded use cases
Each phase included a dedicated cycle of planning, development, testing, and validation with the client.
The Team Behind the Project
The project was delivered by a compact, cross-functional team consisting of a Project Manager, responsible for planning and stakeholder coordination, a Business Analyst, who gathered requirements and mapped the process flows, and Automation Engineers, who implemented the solution and managed system integrations. Their agile collaboration and flexibility, including rotating roles based on availability, were key to the project’s efficient execution.
Tangible Results: Nearly €1M Saved in Phase 1 Alone
The first phase alone delivered close to €1M in cost savings. While Phase 2 was more focused and delivered fewer savings, the return on investment remained strong. Even more importantly, the automation introduced consistency and predictability into the WO process — two qualities that significantly enhance operational control.
Not Just for Telecom
Although the solution was developed in a telecom context, the concept is highly adaptable. Any industry that:
- – Relies on physical infrastructure
- – Uses automated alerts from connected devices
- – Dispatches field teams for issue resolution
…can benefit from a similar approach. This includes utilities, energy, logistics, and more.
Lessons Learned and Final Thoughts
Developing the delay algorithm was the most complex part, requiring fine-tuning across numerous parameters. System integration was also a challenge, but one that we’re used to managing.
This project clearly demonstrates that even partial automation of a well-defined process can lead to substantial operational savings, especially when it’s carefully aligned with real business needs and system capabilities.
If your organization is struggling with high costs from reactive field interventions, it’s worth exploring how intelligent automation can help you act smarter — not just faster.
Want to talk about automation in your operations? Let’s start the conversation @ info@realworld-systems.com